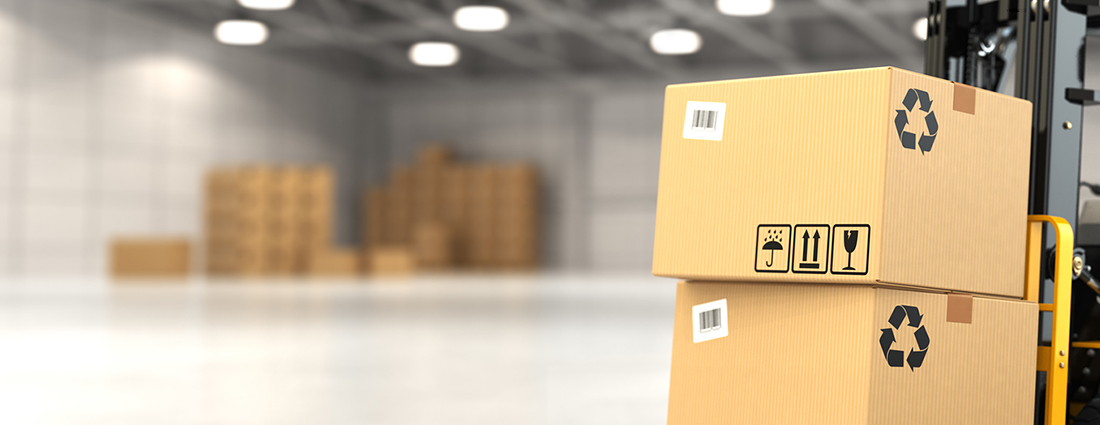
在庫をコントロールする方法を本章よりご説明させて頂きますが、本題に入る前に「経済的発注数量」について少しお話をさせて頂きたいと思います。
この「経済的発注数量」とは何?ということになりますが、英語にするとEconomic Order Quanity、略してEOQ…申し訳ありません、ますます分かりにくくなってしまいました。
これは在庫にかかわる費用を最小限にするための発注数量のことです。つまりいくつ発注すれば最も経済的なのかということを求めるのです。求め方は1回の発注にかかる費用と在庫維持費用を設定し、発注回数に1回あたりの費用をかけて行きます。
発注数量が多ければ当然在庫が増え在庫維持費用が増えます。かといって発注数量を少なくすれば、発注回数が増える為、発注費用(人件費・通信費等)が増えます。この発注費用と在庫維持費用を足して最も少なくなるポイントを導き出します。実はこの経済的発注数量という単語は在庫管理の本を読めばまず間違いなく説明されています。
またかなりの確率で曲線グラフ付きで解説がありとても重要なことのようです。けれど私はこの経済的発注数量を上手に活用されている企業を見たことがありません。そこで私が「上手に活用する方法をお教えしましょう!」と言いたいところなのですが、本音はその全く逆です。活用しない方がよいと思います。
理由は単純で、この在庫維持費用、また発注1回にかかる費用を正しく設定することが非常に困難である為です。この2つのパラメータを正しく設定し、またメンテナンスしていかないと、この経済的発注数量と言うのは意味をなしません。あなたがもし会社でこの2つの費用をアイテム毎に設定し、管理しなさいと言われたらどうでしょう。この数字を管理するだけの仕事であれば可能かもしれませんが、その他の管理や作業に振り回されている忙しい毎日の中ではっきりいって不可能だと思います。古くから存在するこの「経済的発注数量」。だまされたと思ってあなたの会社でも試してみてはいかがでしょうか。
本題に入る前の序文の予定がすごく長くなってしまいましたので、在庫コントロールについては次節にて。
それではいよいよ在庫をコントロールする方法をご紹介していきたいと思います。
ところで在庫をコントロールするとは具体的にどういうことでしょうか。「ノートパソコンを今月10台発注しよう」というのは100%自社の意思決定で行えますが、「ノートパソコンの在庫が10台あるので、今月は10台全て売り切ろう」なんてことは目標として掲げることは出来ても、目標、予測の域を超えることは不可能です。可能であればたちまち億万長者です。
結局在庫をコントロールする上で自社で100%決定出来るのは発注だけです。出荷は予測は出来ても自社でコントロールすることは不可能です。「入ってくる在庫は決定出来る、出ていく在庫は決定出来ない」これが在庫管理を難しくしている大きな要因の一つです。 しかし逆に、出ていく在庫さえ予め把握出来れば在庫がコントロール出来るようになるということでもあります。
3章6節でAランク商品は手間をかけて定期発注方式を行いましょうと説明しました。この定期発注方式は発注タイミングは定期的ですが、発注数量は不定量です。よって欠品せず、過剰もないように次回入荷日までの出荷数を予め予測して発注数量を決定する必要があります。経験と勘に頼るのも一つの有効な手段です。場合によってはコンピュータの計算で決定される発注数より適正なこともあります。しかし、アイテムが数千点ある場合や出荷変動が激しい場合は、計算式に頼る方が簡単で確かな方法です。
例えば下記のようなケースを想定してみましょう。毎週月曜日に発注して、翌週の月曜日に入荷される運用のケースです。本日が8日月曜日だとした場合、この日の最適な発注数量はいくつでしょうか?
このような場合、実は簡単な計算式で最適な発注数量を算出可能です。
まず8日月曜日の発注日から次回入荷日までの出荷予想数を計算します。ここでは前週の1日から7日までの出荷数の合計442を出荷予想数と設定します。次に今回の発注分が入荷される15日月曜日から次回入荷までの出荷予想数を計算します。こちらも先程と同じく442となります。最後に発注日の在庫数638と安心在庫を200と設定して、ここまでのそれぞれの数値を下記の計算式で計算します。
A | 注文日から次回入荷日までの販売予測数 | 442 |
B | 今回発行分の入荷日から次回入荷日までの販売予測数 | 442 |
C | 特売数 | 0 |
D | 注文日当日在庫数 | 638 |
E | 安心在庫 | 200 |
注文数=A+B+CーD+E
A(442)+B(442)+C(0)ーD(638)+E(200)=446となります。
8日月曜日に発注数する数量は446です。特売数はセールや年末などで出荷数が大きく増える場合などに任意に設定します。過去のセール時のデータを活用 すれば簡単に分かると思います。安心在庫は欠品をなくす為に設定するのですが、100%欠品をなくそうとするとどうしても余分に設定してしまうので、10週に1度の欠品は仕方ないとある程度の欠品を前提に計算して計上します。この欠品の許容率は自社の戦略方針で決定すればいいと思います。多少在庫を余分に持ってでもお客様に迷惑をかけてはならないといった方針であればそれも結構でしょう。
以上、定期発注方式による発注数量の方程式をご紹介しました。これによりある程度の精度で在庫をコントロールすることが可能になります。発注数量を検討する場合の計算方法(需要予測ともいう)は今回説明した計算方法以外にも実は沢山あるのですが、また次の機会にご紹介させて頂きます。
需要が安定しない場合、需要変動を前提にした発注方式が必要となってきます。需要が安定的に推移しないとなると問題となってくるのが、「定量」や「定期」といった定められた値です。需要の変動が激しい場合、定量や定期に頼って発注を行ってしまうと、欠品の恐れもあり、過剰に在庫を持たざるを得なくなってしまいます。そこで検討されるのが「不定期不定量発注」です。
この方式はまず発注点を定め、在庫が発注点を割った時に、その時必要な数量を発注するというものです。
よって発注数量も発注時期も不定となります。
ただしこの方式は管理対象となるアイテムの出荷量、在庫量を常に監視し、発注点を割っていないかどうかのチェックも必要となる為、アナログ管理では不可能です。在庫アイテムが少なければ可能かもしれませんが、通常はまずアナログでの管理は無理と考えて下さい。
不定期不定量発注方式を行う目的として、当然在庫を出荷変動に対応させるということが挙げられます。しかし、在庫を数量で見てしまうと実は出荷変動には対応出来ないのです。ではどのようにして出荷変動に対応可能な発注を行うのでしょうか。
詳しくは次節でご説明させて頂きます。
需要が安定しない出荷変動の激しいアイテムを適正に在庫管理するとなると「不定期不定量発注」が検討されます。この管理方法を用いる場合、在庫を今まで通り数量で管理してしまうと思うようにいきません。
例えばリンゴが500個あったとします。このリンゴがたった今100個出荷されて400個になりました。しかしこの400個が多いのか、少ないのか、発注が必要なのか、必要ないのか分かりません。いつも出荷を担当している現場の担当者は経験と勘で分かるかもしれません。しかしこのリンゴ400個という数字は意味をもっていません。よく数字は「言葉」であると言われます。言葉である以上、標準語で話す必要があります。そして意味を持たせる必要があります。
発注管理において発注点を持たせる方法がよく用いられます。
「リンゴ200個になった時点で発注する」これにより少しは400個という数字に意味を持たせることが出来ました。
何故なら「リンゴがあと200個出荷されたら発注しないといけない」という言葉・意味を持っているからです。しかし、本節冒頭にて出荷変動の激しいアイテムを不定期不定量で管理と述べています。もし明日300個の出荷が発生し、次の日200個の出荷が発生したらたちまち欠品です。
発注点という数量を定めてしまった時点で数量が固定化されてしまい、激しい出荷変動に耐えられません。欠品を起こさずに発注点で管理を行おうと思うと、当然出荷変動に合わせて随時このパラメータを変更・メンテナンスしていく必要があり運用が破綻してしまいます。
上記の様なことですから結局数量では管理出来ないことが分かりました。
それでは何で管理するのでしょうか。在庫日数で管理します。在庫日数とはリンゴを何日分保有するかということです。3日分持つと決めれば発注数量は3日×1日当たり平均出荷数となります。リンゴの在庫が今何日分ある、今度の発注は5日分発注しようといった具合に数字に意味をもたせることができ、分かりやすくなります。出荷数量、発注数量は常に変動しますが、日数は変わりません。これにより在庫削減会議の席でも「リンゴは今3日分の在庫があります。来週より2日分に変更します。」と上層部の方にも伝わりやすい標準語で話をすることが出来るのです。
在庫を日数で管理する。まずはこのことを頭に保管しておいて下さい。
以前の節で売れ行き(出荷数量)は予測することは出来ても完全にコントロールすることは不可能だと述べました。在庫は入庫と出庫の簡単な差ですので、入庫数量、出庫数量が自在にコントロール出来れば恐らく誰も頭を悩ませることはないでしょう。
予測出来ない売れ行き。複雑な需要予測計算を持ってしても、見事に外れるこの悩ましい売れ行き(出荷数量)はどのようにして把握することが出来るのでしょうか。小売店であればPOSの販売情報を得ることで有る程度正確な売れ行き状況を把握することが可能です。
では下記のような場合で少し考えてみましょう。
この様な場合、メーカー側の立場から見ると、どこから売れ行き情報を得ればよいのでしょうか。
普通に考えればメーカー倉庫から卸売業者に出荷が行われたデータを参考にすると思います。しかし、これではどこの小売店に商品が販売されたか、どれだけエンドユーザー(最終消費者)に購入されたかは全くわかりません。メーカーにはどのようにして売れ行き情報が伝わるのでしょうか。よく売れている商品の場合を例にして下記の図で説明します。
よく売れている商品の場合、小売店には常に在庫薄状態が続きます。当然卸売業者には常に発注がいき、そのままメーカーに発注がどんどん行きますので、メーカーは喜んで商品をじゃんじゃん作ります。しかし売れなくなるとどうなるでしょう…
ユーザーの購買意欲(ニーズ)がなくなると小売店は在庫がなくなり次第、次の発注を行うことを止めます。そして卸売業者に発注停止が伝わるまでに数週間かかります。しかしその間卸売業者はメーカーに納品依頼をかけているのです。
当然メーカー側もじゃんじゃん作っているのです。メーカーへの注文が減るのはなんと小売店での売れ行きが落ち始めてから1ヵ月以上かかる場合もあるのです。メーカー倉庫、卸売業者には不良在庫の山ということになります。
このようにユーザーから距離の遠い立場である程、リアルタイムに売れ行きを把握しにくく、不良在庫を抱えるリスクが高いということになります。一時期流行ったSCM(サプライチェーンマネジメント)もこのような問題に対処する為でもありました。
ではこのような流通ギャップをどのようにして埋めるのか。方法はいくつかありますが、主な方法は以下の3点です。
いずれにしても売れ行き(出荷数量)は完全にコントロールすることが出来ないので、いかに正確な情報を手に入れるかを検討する必要があるということです。