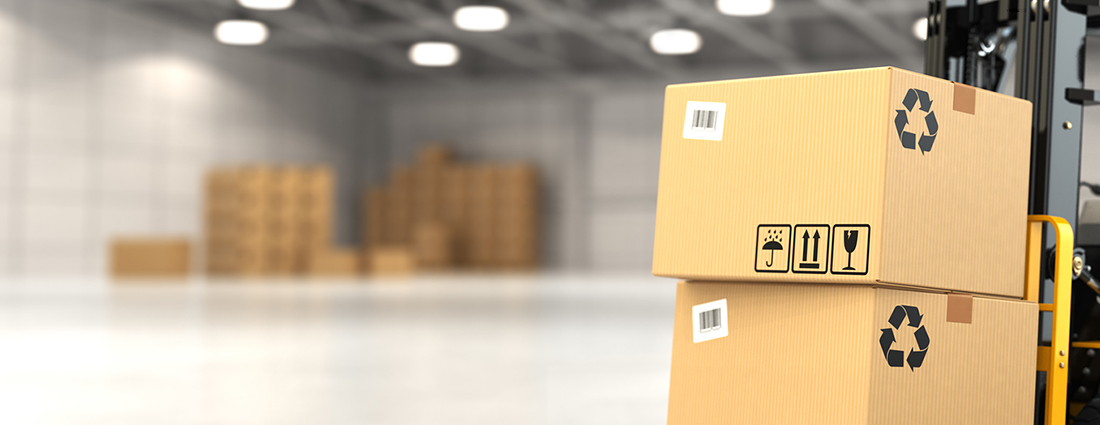
まずは経営者の方、倉庫に行って実際に在庫を見て下さい。
倉庫担当者に任せきりでもう随分と倉庫は見ていないという経営者の方が実に多いのです。数字の在庫だけを見ていては本当に在庫が問題であると認識する危機意識レベルにまで達しません。
まずは在庫を自分の目で確認しましょう。そして在庫過剰の問題を肌で感じ、危機意識レベルの高いうちに死蔵在庫を廃棄しましょう。人間はどうしても時間の経過とともにその時感じた感情は薄れてしまいます。
「このままではまずい!」と心の熱いうちに思い切って死蔵在庫を廃棄するのです。賞味期限などない商品だとどうしても「いつか売れるかも」とか「いつか値段を下げてでも売ろう」などと考えてしまい、「もったいない意識」が働いて廃棄することが出来ません。売れない商品はそこに置いておく方がもったいないのです。管理コスト、倉庫費用、人件費、などもったいないことばかりです。
まずは必要なものと不要なものを分けて整理をしましょう。
すごく初歩的で簡単なことですが、これを真剣に行うだけでかなりの在庫が削減されることは間違いありません。
どうしても捨てようかどうか迷うアイテムがあれば、その迷った日を書いた札を置いておくとよいでしょう。迷ったら置くので「迷い札」と勝手に命名しました。もし売れれば札を捨てて下さい。「迷い札」の日付から90日経過してもまだ札が置いてあるようであれば、廃棄すると運用を決めてしまえば気持ちも楽になります。
迷える経営者の方々、まずはお試しください。
皆さん、5Sという単語をご存じでしょうか?
おそらく製造業の方であれば皆さん当たり前のように見聞きする単語だと思います。しかし製造業や工場・倉庫関係以外の方になると意外と知らない方も多いのではないでしょうか? また単語は聞いたことはあるけど、内容についてはよく分らないという方も多いはずです。
5Sとは整理・整頓・清掃・清潔・躾を徹底することで業務を改善しようということです。
私達はこの5つのSに、継続出来る仕組み作りを付け加えて6Sをお客様にお勧めしています。
この6Sを徹底することで工場・倉庫を安全・見える化します。工場・倉庫の見える化は在庫を正確に管理する上では決して忘れてはならない重要事項なのです。発注方式や在庫管理のシステム化にばかり重点がおかれ、倉庫を見ると製品が直置きされたままといった企業様を多く見てきました。どんなに優れたシステムを導入したところで、現場改善がおざなりになっているようであれば、その企業の在庫管理は完全には最適化されません。
我々は優れた6Sの手法を製造業や工場の方だけではなく、小売業、卸売業の方にも強く意識して取り組んで頂くようお勧めしています。今まで見えなかった問題点が見えるようになり、在庫削減に向けて大きく前進出来るはずです。
6Sを行い整理整頓を行う上で重要なのが看板作戦による倉庫の見える化です。
看板作戦では「3つの定」と呼ばれる要素を見える化することにより現場での迷いを撤廃します。
[1定] 定位 |
■定められた場所に:場所表示 まずは場所を表示します。ゾーン、列、段が一目でわかるように看板を取り付けます。 |
[2定] 定品 |
■定められた品物を:品目表示 次に品目を表示します。固定ロケーションの場合は棚に直接品目看板を取り付けます。 フリーの場合はアイテムに直接品目ラベルを貼る、もしくはマグネットなどの取り外し可能な看板を利用することも有効です。 |
[3定] 定量 |
■定められた量だけ:量表示 この定量を見える化されている倉庫はなかなか少ないのですが、その名の通り量を見える化します。例えば発注点を記載したり、棚にラインを引いて高さで量を見える化するなどの工夫が考えられます。 |
このように場所、品目、量の「3つの定」を見える化するだけでかなりの業務効率化が図れます。
「アイテムが多すぎて無理」「すぐに元に戻るからやっても無駄」「場所を固定出来ない」など色々な理由で看板作戦が行われていない倉庫は多いようです。しかし最初は大変ですが、必ず効果は表れます。
迷いがなくなる→ミスが減る→作業効率UPといった相乗効果により、思った以上の効果を得られることでしょう。
不良在庫を断腸の思いで処分し、現場6S、看板作戦により整理整頓された倉庫。以前に比べ随分と見違えた倉庫を眺めながら次はいよいよ商品のランク分け…と行きたいところですがちょっと待って下さい。確かに商品をABCでランク分けしてロケーションや発注方式をランク別に管理するというのは在庫改善の定石です。しかし、このABCランク分けを全てのアイテムに対して行うということは、実は非常に不効率なのです。
ABCランク分けは注意して管理すべき在庫に対してのみ行えばいいのです。
ということでまずは在庫を下記のように大きく3つに区別しましょう。
○常備在庫品
その名の通り常に在庫を持っておかなくてはならないアイテムのことです。流通業で言えば定番商品、製造業などではライン生産の製品用部品など、在庫が切れると損失となる重要アイテムです。
○特別注文品
よくいうお取り寄せ商品等です。在庫はないけれども取り扱い商品である為、注文や依頼は発生します。注文を受けてからメーカーに取り寄せ、そのまま出荷するといったアイテムがこの分類に入ります。特別注文品と設定されたアイテムは倉庫内に在庫として保管してはいけません。
○常備外在庫品
経営戦略による政策在庫の売れ残り品、不良品やクレームによる返品などが常備外在庫品です。また、以前は定番商品だったが、定番から外れた流行遅れ商品なども、常備外在庫品となる可能性大です。常備外在庫品をそのまま放っておくとデッドストックとなります。
以上のように大きく3つに在庫を区別します。この中でABCランク管理が必要な在庫は当然「常備在庫品」です。
特別注文品や常備外在庫品をABCランク分けしても苦労の割にはあまり役には立ちません。在庫を切らしてはいけない「常備在庫品」に対して集中的に管理を行うことで効率的な改善が可能となります。
前節でABCのランク分けは常備在庫品に対してのみ行うことで効率的に管理できることをご説明しました。では在庫をABCランクで管理するとは具体的にはどういうことでしょうか。頭でぼんやりとはイメージが出来ても、実際現場の業務に落とし込むにはどのように行えばよいのか具体的な策が見えてこないといった方も少なくないのではないでしょうか。
在庫のABCランク別管理を簡単に説明すると「売れている順に並べて手間をかけて管理するアイテムと手間を省いて管理するアイテムに分けてメリハリをつけましょう」ということです。
この売れている順というのは数量で見る場合と金額で見る場合とがあります。どちらで見るかは各企業の判断ですが、私の今までの経験上、商品の回転率が勝負といったアイテムが中心であれば数量で見た方がいいでしょうし、ブランド品など高価なアイテムが中心であれば金額で見た方が効果的な場合が多いようです。例えばコンビニのおにぎり等、回転率が勝負のアイテムは金額ではなく、数量で見た方がよいでしょう。
またもう少し章が進んでいくとピッキング効率を上げるために商品をABCランク分けします。しかしこの場合、ランク分けに使用する数字は出荷数量でもなく売上金額でもありません。では一体何の数字で判別するのでしょうか?
正解は・・・今後の章でお話させて頂きます。
さて、皆さんも既にご存じかとは思いますが、ABCランクの定義は下記の図のようになります。
○パレートの法則
皆さんパレートの法則をご存知でしょうか。難しく説明するとイタリアの経済学者ヴィルフレド・パレートが発見したべき乗則です。これを在庫管理に関係させて簡単に説明すると「全体の80%を占める売上は20%のアイテムが生み出している。」となります。つまりAランク商品というのは全アイテムの20%になります。このわずか20%のアイテムを集中的に管理すれば、売上の80%は適切に管理されることになるのです。
次にABCランク別の管理方法を見てみましょう。
売上上位のAランク商品は欠品になった時の売上に対する影響は大きい反面、在庫が増えすぎた場合もまた経営に多大なダメージを与えることもある為、十分に手間をかけて注文を行います。Bランク、Cランクについては出来るだけ、簡単な注文方式を採用します。
次節ではそれぞれのランクにあった注文方式について説明します。
さて、在庫管理勉強会も発足から早いもので1年2ヵ月となりました。お陰さまで色々とご意見やご感想も頂いており、大変感謝しております。中には文字が小さい、文章が長いなど厳しいご意見も頂いておりますが、出来るだけ改善をしていければと考えております。ご指摘感謝いたします。そして1年間でまだ注文方式をやっているのかと思うと、後何年かかるのだろうと真面目に不安にもなります。今後は少しペースをあげていければと考えておりますが自信はありません。
前節で常備在庫品をABCランク分けいたしました。続いてはそれぞれのランクにあった発注方式を用いて、メリハリのある注文を行いたいと思います。まず一般的な発注方式をご紹介いたします。
定期発注方式 | 毎週一回、月一回と決められたタイミングでその時必要な数量を発注する方法。 |
定量発注方式 | 発注点、発注量を定め、毎回決まった数量を発注します。例えば発注点が100で発注数が200であれば、在庫が100を切ったタイミングで200個を発注します。 |
ダブルビン方式 | 例えば名刺。100枚入りの名刺が2箱あり、1箱目がなくなると1箱追加発注します。 |
一般的でよく使用されている方式としては上記3つ程ではないでしょうか。私の認識ですので、もしかすると違うかもしれませんが。あとは上記の組み合わせで定期定量発注方式や不定期不定量発注方式などありますが、今回は冒頭で述べたペースUPの為、割愛させて頂きます。
定期発注方式の特徴は決まったタイミングで発注を行うという点と、数量が不定量であるという点です。この不定量というのが難しく、次回発注タイミングまでに欠品もせず、余りもせずという需要予測なる考え方が含まれる方式となります。よって3つの中では一番高度な方法ではないでしょうか。
定量発注方式は発注点方式とも言われます。商品毎に発注点(安全在庫)を定め、発注点を割ったら決まった数量を発注します。商品毎に発注点、発注数量の2つのパラメータを設定しなくてはならないのが特徴です。一見大変そうですが、パラメータを設定してしまえばあとは比較的簡単に管理が行えます。ただしパラメータの定期的なメンテナンスは当然必須となります。
ダブルビン方式は2つのビンがあり1つのピンが空になったら1ビン発注するとといった方式です。ご家庭で使用される醤油やお米、オフィスで使用するコピー機のトナーなど身近でよく利用されていると思います。
次にABCランクと上記3つの注文方法を関連付けしてみましょう。
商品ランク | 発注方式 | 管理 |
Aランク商品 | 定期発注方式 | 過剰・欠品にならないよう手間をかけて管理 |
Bランク商品 | 定量発注方式 | 過剰・欠品にならないよう少し手を抜いて管理 |
Cランク商品 | ダブルビン方式 | 在庫が切れないように出来るだけ簡単に管理 |
つまり売上上位20%の商品については細心の注意を払って手間がかかっても過剰、欠品にならないようしっかり管理します。上位20%〜40%の商品については発注点、発注数を決めておいて、Aランク商品よりは簡単に管理します。売上40%以降の商品については出来る限り手間をかけずに管理します。
全ての在庫アイテムについて細心の注意を払って管理出来れば理想かもしれませんが、現実的ではありません。在庫数のコントロールは発注でしか行えません。発注業務は在庫削減のドライバと言えます。在庫削減=発注業務改善といっても過言ではありません。是非発注にメリハリをつけ、在庫をコントロールしてみて下さい。
本章の最後に在庫を管理する上で今まで説明をさせて頂いた内容の他に重要なポイントを2つご説明します。
この2点、実に当たり前のことの様ですが意外に見過ごされている場合も多いのです。
その理由としては、在庫管理という企業戦略が社内であまり重要視されていない、もしくはそもそもそのような戦略は存在しない等の理由で、在庫管理を確実に行う為の運用ルールが社内、倉庫に存在しない。また有能な推進リーダーの不在等も主な理由です。倉庫業務において、情報を誰がいつ記録し、どこに報告し確認するのかなどの基本的なルールはもちろん、社内での研修、返品処理等のイレギュラーな対応の明確化は必ず大きな効果を得られます。
2点目の入荷出荷データを正確に記録するについてですが、こちらに関しては倉庫管理システム(WMS)等の高価なシステム投資は不可能といった要因が最も多いのではないでしょうか。確かに正確に入出荷を記録するとなるとリアルタイム性が必要となり、ハンディターミナルやバーコード等を使用した倉庫管理システム(WMS)が必須となってきます。そのような事は企業側も十分に理解はしているのだけど、安い投資ではないし、ましてや企業内であまり重要視されていない戦略となるとそのような予算は付きません。
しかし我々は今後在庫削減戦略は販売戦略等と肩を並べる程に企業の中心課題として位置づけられると確信しております。高価なシステムを導入して在庫削減、物流改善に失敗してしまうのは恐ろしいことですが、この在庫管理勉強会で説明させて頂いているような基本的なポイントを抑えて、焦らずじっくりと進めていけば必ず企業のプラスになる大きな効果が得られると信じています。
次章では在庫を上手にコントロールする方法をご紹介いたします。